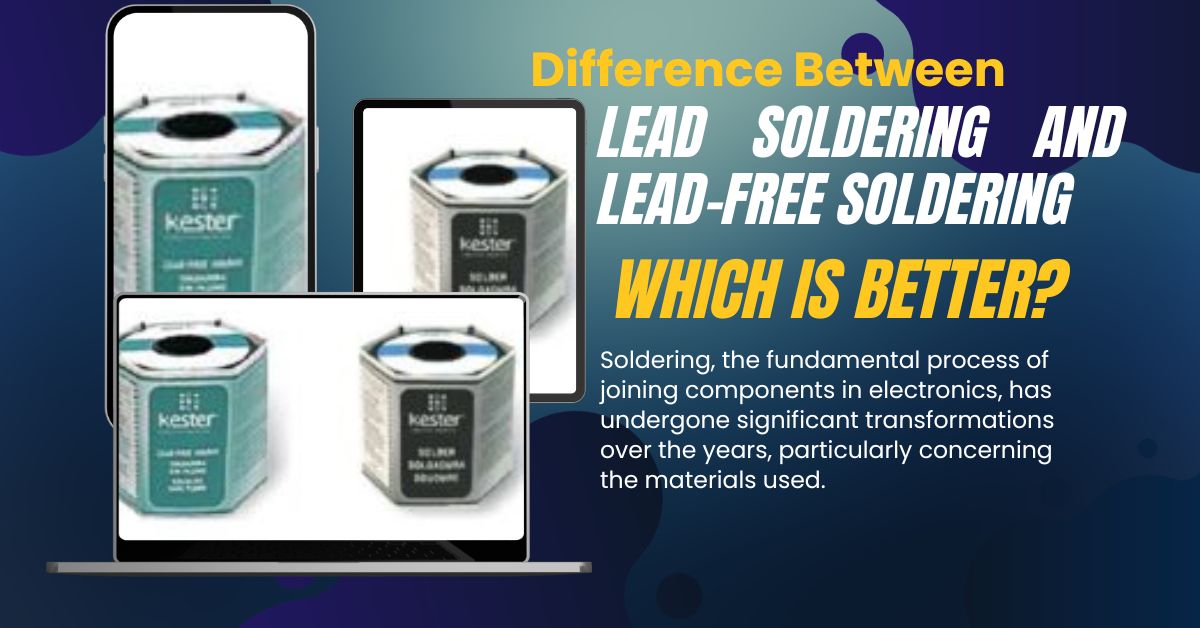
Soldering, the fundamental process of joining components in electronics, has undergone significant transformations over the years, particularly concerning the materials used. One of the most critical distinctions lies in the choice between leaded and lead-free solder. Let’s delve into the difference Between Lead Soldering and Lead-Free Soldering, implications, and considerations surrounding these two soldering materials in the realm of electronics.
Leaded Solder: Tradition Meets Effectiveness
Composition
Leaded solder traditionally contains a mixture of tin and lead, with common ratios like 60/40 (60% tin and 40% lead) or 63/37. The addition of lead lowers the melting point, improving solderability and flow characteristics.
Advantages
- Ease of Use: Leaded solder melts at lower temperatures, making it easier to work with during soldering.
- Reliability: It forms strong, durable joints and exhibits good wetting characteristics, creating reliable connections.
- Repairability: Leaded solder joints are often easier to rework or repair due to their lower melting point.
Concerns
- Environmental Impact: Lead, a toxic heavy metal, poses environmental and health risks. Improper disposal can lead to soil and water contamination.
Lead-Free Solder: The Move Towards Safer Practices
Composition
Lead-free solder replaces lead with alternative metals such as tin, silver, copper, and sometimes bismuth. Common compositions include SAC alloys (tin-silver-copper) like SAC305 (96.5% tin, 3% silver, 0.5% copper).
Advantages
- Environmental Safety: Lead-free solder significantly reduces environmental and health risks associated with lead exposure during manufacturing, use, and disposal.
- Regulatory Compliance: Many regions enforce regulations mandating the use of lead-free solder in electronics to meet environmental standards.
- Long-Term Viability: Lead-free solder aligns with global environmental initiatives and ensures the long-term sustainability of electronic products.
Challenges
- Higher Melting Point: Lead-free solder typically melts at higher temperatures compared to leaded solder, requiring adjustments in soldering techniques and equipment.
- Reliability Concerns: Achieving equivalent reliability to leaded solder joints requires precise control of soldering conditions and proper handling techniques.
Read Also:
- Unveiling the Unseen: Harnessing the Power of Digital Microscopes
- Best Transducerized Screwdrivers and It’s Application & Benefits
Conclusion
The transition from leaded to lead-free solder marks a significant stride toward safer and more environmentally conscious soldering practices in the electronics industry. While leaded solder offers ease of use and reliability, lead-free solder aligns with global environmental regulations and long-term sustainability goals. However, the shift to lead-free solder presents challenges in terms of higher melting points and reliability concerns, necessitating careful consideration and adaptation in soldering techniques. Ultimately, the difference between leaded and lead-free solder depends on a balance between performance, environmental responsibility, and compliance with evolving regulations.